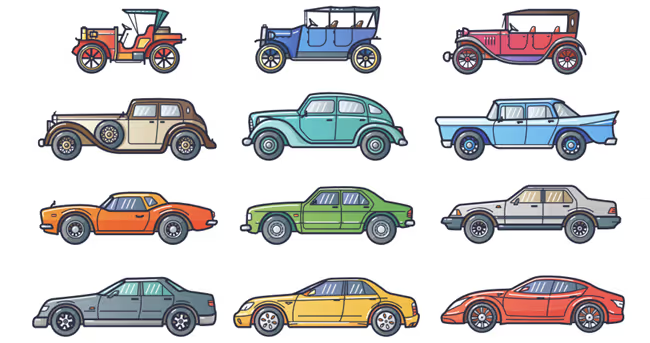
A LOOK AT CURRENT SUPPLY CHAIN ISSUES, HOW WE GOT HERE AND WHAT MIGHT THE FUTURE HOLD
____________________________________________
Supply chain issues facing all sectors of the economy are real and complex. To help understand the current position, here’s a high level view of life before the pandemic, the COVID effect and what’s likely to change.
Which industry has had the biggest impact on manufacturing, supply chain logistics and delivery of goods to consumers in the last 50 years? Automobiles! In the beginning, Ford Motor Co. said we could get any color car we wanted – as long as we wanted black. Assembly lines rolled, stamped and shipped.
Keeping Up With Demand
Following World War II, U.S. manufacturers pivoted their mass production capabilities from military to consumers. This presented a very real challenge – how to transition mass production capabilities to the new task of offering consumers the choices they wanted with different styles, colors and options.
You may recall going to a dealer, ordering a car with custom options, waiting some number of weeks and then scheduling a time to take delivery of a fully customized vehicle directly from the factory. Similarly, homeowners once selected large appliances for their kitchens in then-fashionable colors like avocado green or harvest gold. Retailers placed orders with manufacturers and delivery followed.
From the 1940s to the late 1970s, consumers were trained in this process. They learned to expect lead times and plan accordingly. Manufacturers had to hold large amounts of raw materials and inventor in advance of orders. Many took on the job of manufacturing all required parts. One factory fed parts to the next. Inventory required cash (and lots of it), physical space and weighed on balance sheets by current measures.
We’ve all the heard the saying, “Good, Fast, or Cheap – Pick Two.” With the effort to provide consumers more options, lower prices and faster delivery, quality began to suffer. The ‘Made in America’ tag line lost some of its luster.
Toyota Drives the Change
Meanwhile in Japan, post-World War II manufacturers faced essentially the same problem – transitioning mass production capabilities to consumers. Management at Toyota is largely credited with a creative solution. Internally referred to as the Toyota Production System [TPS] in the 1950s, it was adopted by many others and evolved into a process called Just in Time (JIT).
Today, we know it worldwide as lean manufacturing. What TPS did that was so radical at the time was move inventory to the production line. That meant workers didn’t have to wait on parts to build cars.
The effort solved production lags that plagued U.S. plants. It also reduced inventory and created efficiencies by working with suppliers for sub-assemblies. Using subassemblies and consignment, Toyota reduced its need for on-hand inventory and shifted some of the financial burden to suppliers. At the same time, it improved its own ability to build to order.
The result was higher quality, lower cost vehicles in ready supply. It seemed like overnight consumers could select all three – fast, good and cheap!
Many U.S. companies were slow to adopt JIT principals which delegated decision-making to the factory floor as opposed to siloed executives. The delay in accepting these competitive processes proved costly for automakers for several decades.
JIT Takes Over
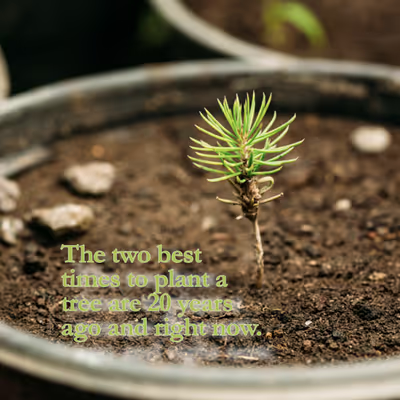
Today, evolutions of the JIT model have been adopted in most every vertical where manufacturing is required. The 1980s and early 1990s saw a meteoric rise in adoption of JIT processes as the exploding tech sector found insatiable demand for the plethora of all new computing devices. In a 1990 poll, 98% of customers expected “JIT treatment.” By 2001, 92% of manufacturers described JIT as critical. For the most part during this time, margins were higher, demand was strong and factory floors were humming. JIT was doing its thing, and all was good.
Forecasting demand became an important part of keeping the lines moving. Consumers and businesses alike were solidly and globally entrenched in plan for forecast, build to order integrated supply and logistic webs. Current generations are now trained to expect what we want, when we want it, the way we want it.
That doesn’t mean we’re spoiled (though some of us maybe). Market drivers trained us in this behavior just as they did generations before us. We’re accustomed to introductory pricing offers, rapid product cycles, end of life discounts, overstocked items and grey market outlets all inducing us to buy this quarter to meet current fiscal year objectives. What many of us didn’t know was just how dependent we had become on the precise behind the scenes coordination this intricate dance required.
It Isn’t Foolproof
Like all systems, JIT has proven to be vulnerable when shocked. It’s highly sensitive to external environment and factors. Any disruption in supply of a single component could have a material impact on delivery of the finished good. We’ve seen this time and again, mostly with regard to minor inconveniences affecting a single shipment, product offering or individual manufacturers.
- The different shocks that can impact JIT include:
- Demand – Changes in customer behavior – radical shifts up or down for products
- Supply – Interruption in delivery of material or volatile pricing
- Transportation – All manufacturing is predicated on ability to move goods
- Geopolitics – Tariffs, trade disputes, war, predictability of governments and regulations
- Finances – Currency exchange, interest rates, availability of capital
- Natural disasters – Earthquakes, tsunamis, drought
- Life After COVID
Any one of these can have a disastrous impact on a well-oiled manufacturing process. The global pandemic essentially was the equivalent of a perfect storm in the entire manufacturing sector no matter what was built or where. And we don’t yet know all the lasting implications.
The impact to the hospitality technology sector is the same as the rest of the world. We can plan ahead. Capital planning now for expected 2023 projects may not get completed until 2024. Align with your key partners and share roadmaps and intentions now. As before, successful projects will require more thoughtful planning and communications with committed partners. Maybe now more than ever.
We do know supply chain and logistics are essential. Lean manufacturing is a healthier financial model when operating smoothly. These systems have little buffer to withstand shocks and finding resiliency has proven difficult. Companies will again weigh the costs of lost sales due to being out of stock against the write-offs associated with obsolete or unsold inventory.
It’s entirely possible the JIT/Lean model will be disrupted again. Globalism, which has enabled movement of goods across borders, has also exposed chokepoints. For example, drought in Asia has forced semiconductor fabrication facilities, known as Fabs, to reduce production. In July 2022, the U.S. Congress passed the CHIPS and Science Act of 2022 to enable and improve domestic semiconductor manufacturing, design and research, thus localizing America’s chip supply chains. Fabs are expensive to build, requiring skilled workers and raw materials.
It will be years before these investments begin to ship product to market. But as another old saying goes, the two best times to plant a tree are 20 years ago and right now.